昨年後半より進めていましたユニット製作のプロジェクトは大詰めを迎えています。前回記事以降に行ってきた工程を下に記します。
①ヴォイスコイルボビンの配線引き出し部の整線。
・2本の引き出し線を約1cmの間隔とし、耐熱性のあるカプトンテープで固定しました。
②2段で構成する蝶ダンパーのうち、コーン紙側(上段)を仮固定
・ダンパーの仮組みはコーン紙とボビンの接着前に行う必要があります。
・ダンパーの内周には配線通し用の逃がしとなる切れ込みを2か所入れました。
③コーン紙にヴォイスコイルリード線(エナメル線)の引き出し用の穴とフレキシブルワイヤー用の穴をあける。
④コーン紙とヴォイスコイルボビンの接着。
・コーン紙側に設定した糊しろになる部分を約5mm程度にカットし、ヴォイスコイルボビンと接着する。(使用した接着剤はセメダインC)
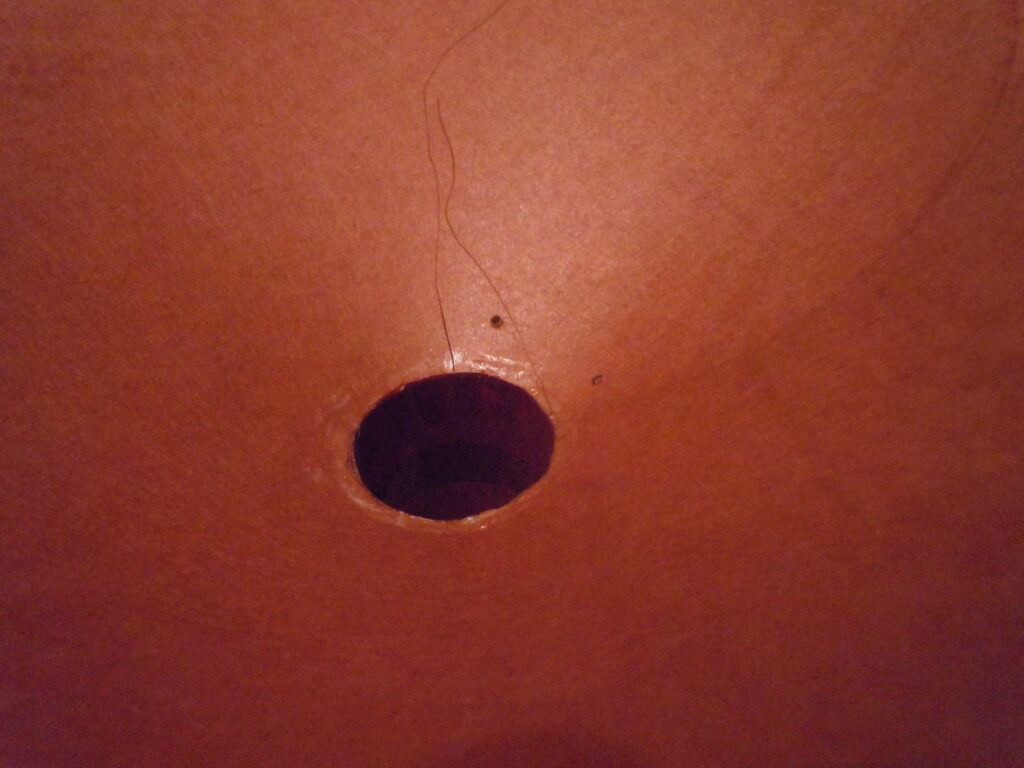
⑤コーン紙とヴォイスコイルを接着したものをヨークのフロントプレートに貫通させ、仮置きする。(上段の蝶ダンパーをフロントプレートにナットにて仮止めする)
⑥マグネット側(下段)の蝶ダンパーをボビンのもう一端に通し、これもフロントプレート裏側にナットで仮止めする。
⑦ヴォイスコイルの巻幅の中央がヨークのフロントプレートの厚さ中心に来るように蝶ダンパーの受けとなるナットの座面高さを調整する。
⑧ヴォイスコイルボビンががヨークのフロントプレートのセンター穴の中心に来るように上下の蝶ダンパー位置を遊びの範囲内で調整し固定する。位置が決まったところでボビンと2枚の蝶ダンパー(ベークライト板)を接着する。(セメダインC)
⑨フレキシブルワイヤーをコーン紙に通し、エナメルリード線とはんだ付けする。
・この時気を抜いていたため接合部のはんだを盛りすぎてしまい、ダマのようになってしまいました。また熱でコーン紙も若干焦げてしまいました。フレキシブルワイヤーとヴォイスコイルリードの接合部はDBボンドというもので固定する自作例が多くあるようですが、接合自体を少し失敗したかなと思いましたので、木工ボンドを接合部と焦げたコーン紙を覆うように塗布しました。(結果としてはこれで何ら問題はないようです)
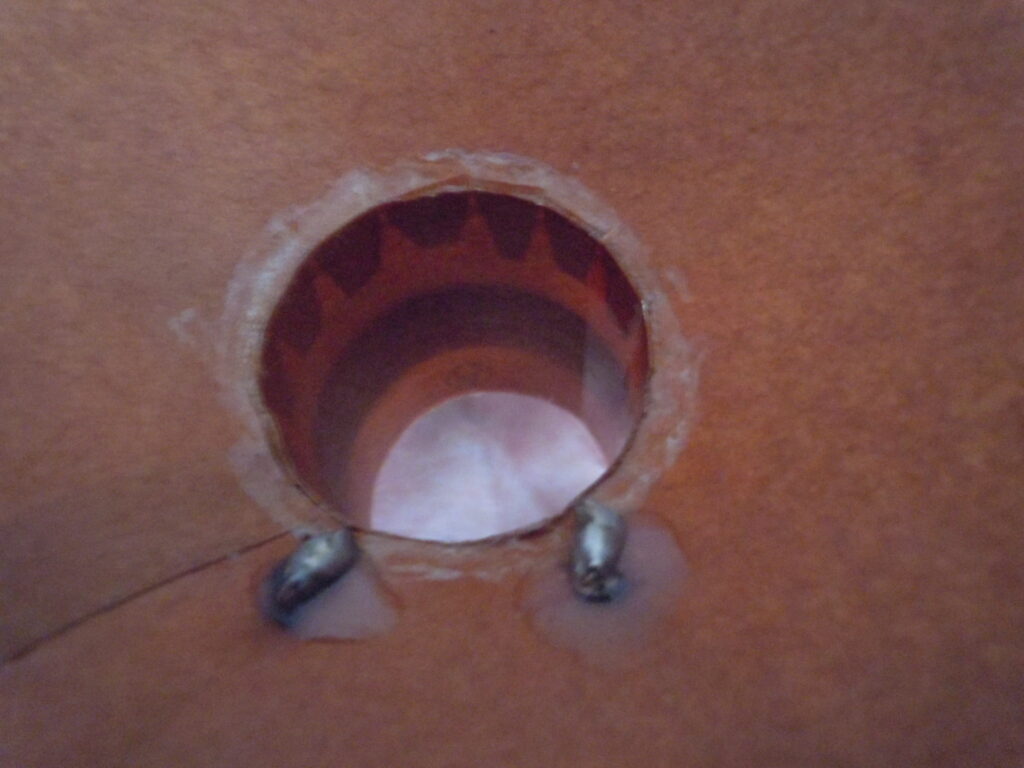
⑩端子台の取り付け
・端子台はヨークのフロントプレートのサイドに設置しました。材料が非常に硬くM3のタップ加工をするのに失敗し、取り付けが1点止めとなってしまいました。全工程完了後接着剤併用で固定する予定です。
・フレキシブルワイヤーとフィールドコイル配線を端子台に接続。
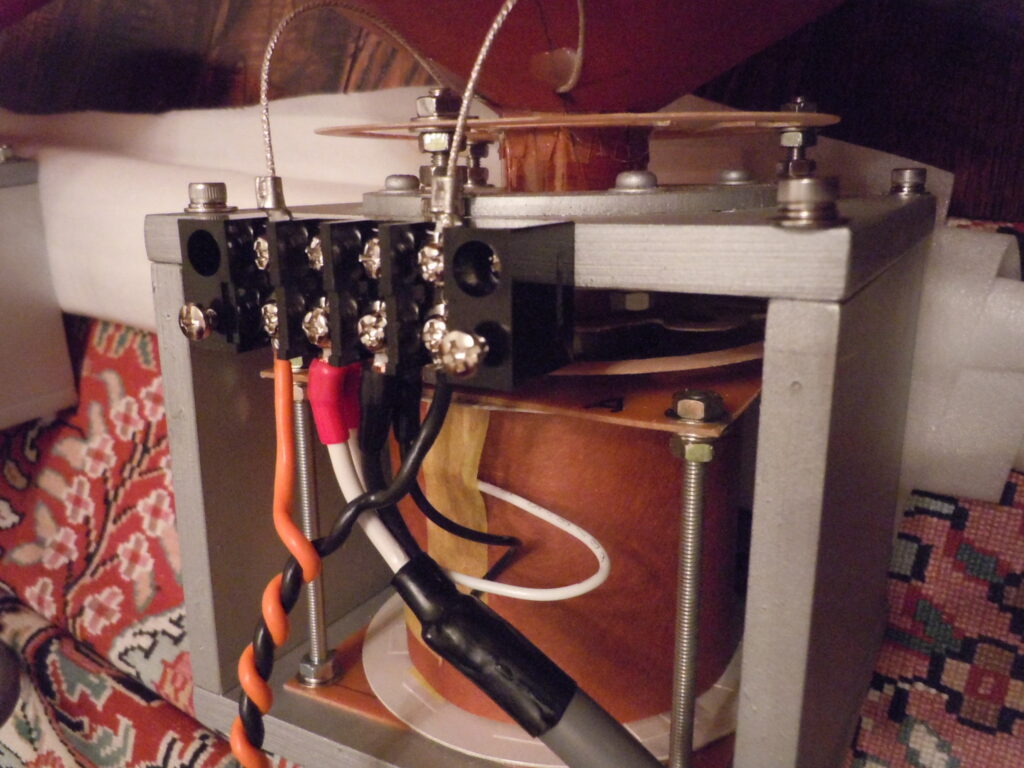
ここまでで一応一連の作業は完了です。
静的な電気的な特性を確認します。
ヴォイスコイル直流抵抗は5.6Ω~5.9Ωで設計時の計算通りです。(インピーダンス8Ω狙い)
フィールドコイル抵抗は2.7kΩでした。(これもφ0.18のエナメル線1kgを使い切る前提から予測していたものにぴったりです)
以前掲載して、今回の自作ユニットへの電源供給のために改造した、フィールド電源供給ユニットを接続してフィールドコイルに供給する電圧と電流を測定しました。
結果は両chともにフィールド供給電圧=約210V, フィールド供給電流=約62mAとなりました。
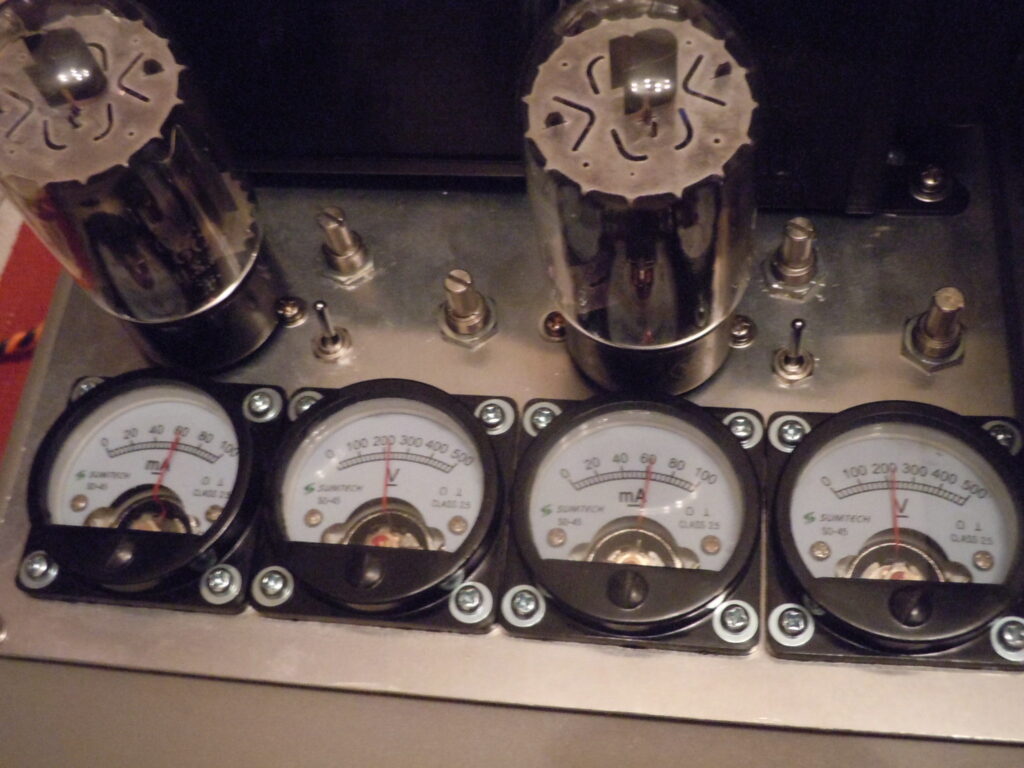
いよいよ音だしです。
マルチアンプ接続になっていたアンプ側の設定を見直してUV845Sをフルレンジ駆動にして
試聴を行いました。
低域が過制動ぎみで量感が足りないものの意外とあっけなく音出しに成功しました。煙を吹いたり、異常なひずみが出たり、ヴォイスコイルタッチによる異音が出たりとかいうトラブルはありませんでした。
低域のオーヴァーダンプの原因を考えました。真の原因はどこにあるかはわかりませんが、手でコーン紙をストロークさせた時に若干抵抗を感じるためこの抵抗感を低減する必要がありそうです。蝶ダンパーの形状パターンを見てみると基本は3方向でボビンを保持していますが、途中で2つに枝分かれしている部分があるためこの枝の片方を切り取り、コーン紙前後方向に対する制動力を削減しました。実際に手で押してみると抵抗感が下がっていることがわかります。
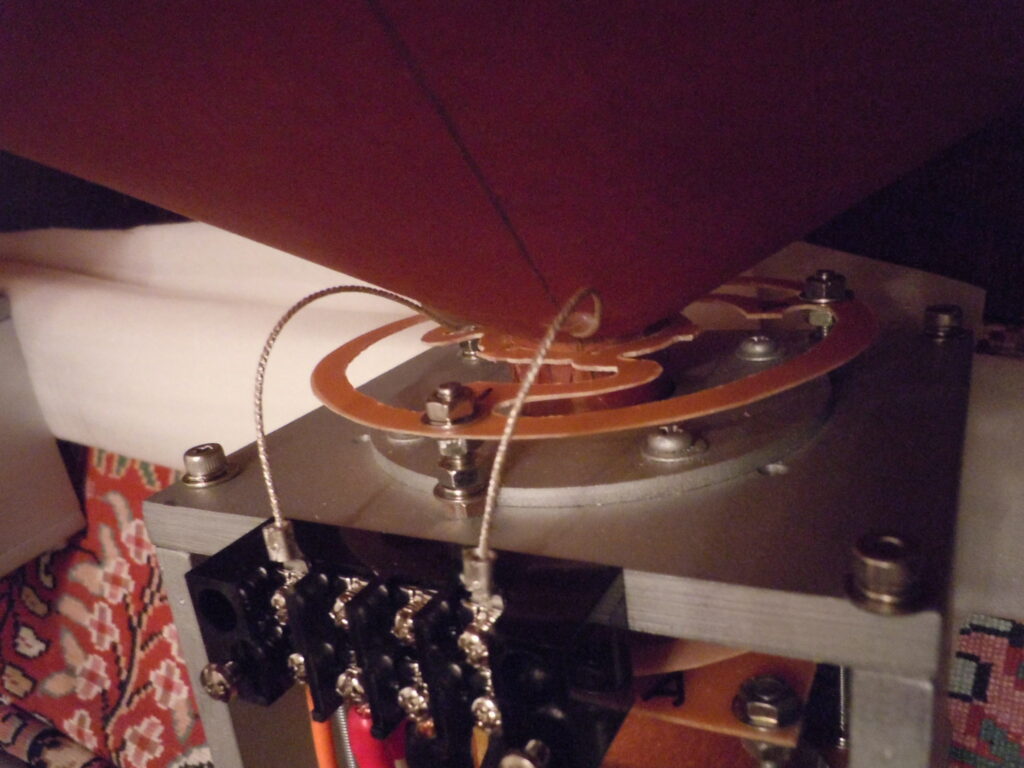
この状態で改めて音出しをしてみた結果、低域の量感はかなり改善され、全体のバランスが向上しました。
最低域までは再生できませんが実用上十分な範囲に入ってきました。フィールドタイプのスピーカーの場合、フィールド電流を少し絞ってやると、低域が少しゆるくなり量感が増すという報告例がたくさんありますので、そこにも調整しろが残っています。また、床置きで箱に入れず裸で鳴らしていることを考慮すると、後面開放の箱や平面バッフルに取り付けて低域の干渉を改善すればかなりの線まで行くのではないかと思います。
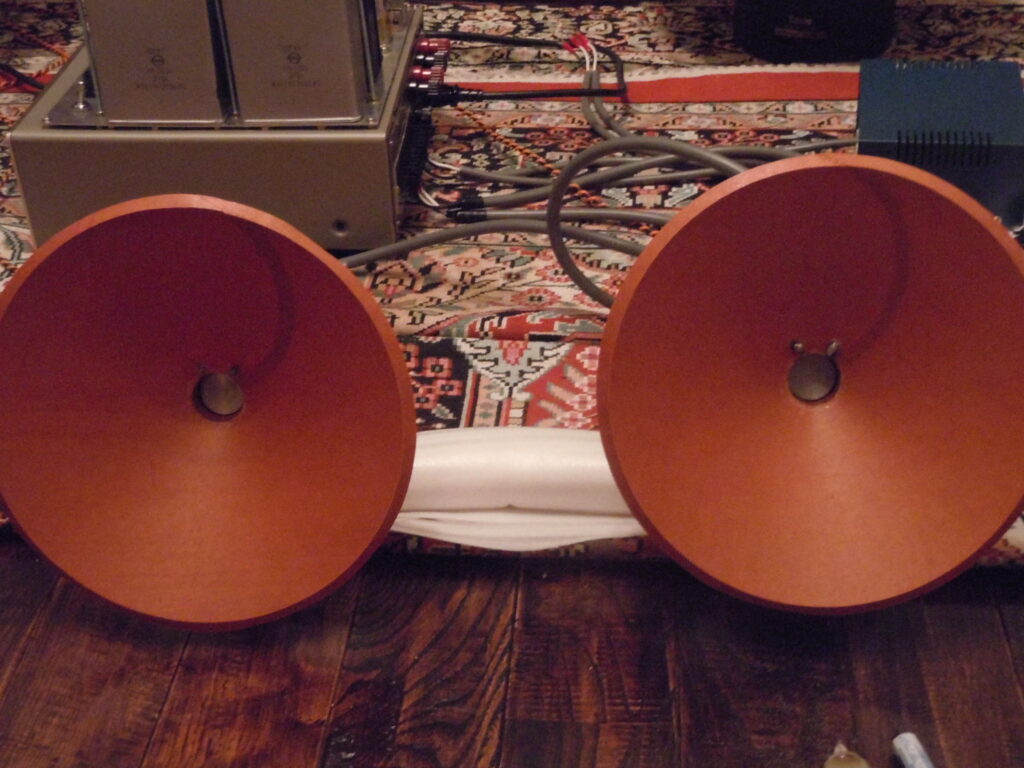
ここまで製作を進めてきて気づいたことを列挙します。
1)今回の設計ではセンターポールφ28,ヨークのフロントプレートの開口径φ31でギャップは1.5mmです。この1.5mmの間隔にボビンとコイルを接触無く組み付けることができないのではないかと心配していましたが、現合合わせの苦労はあったものの不可能な設定ではないということが確認できました。
2)コスト低減のために穴あけはかなりの部分を自分でこなしました。その結果、加工精度の問題であちこちで寸法に狂いがあり穴を長穴にしないときれいに組み付けができなかったり、タップが折れ込んで修復に時間がかかったり、端子台などは修復不能でビス1本止めになったりしました。1穴200円くらいをコストダウンしようとした結果このようになってしまいましたが、次回製作する機会があるのなら精度に関連する穴あけは多少出費がかさんでも業者にやってもらう方ができもよくなるでしょうし、時間を無駄に費やすこともなくなります。今回、ここもあそこも位置ずれという状態で組み付けてきたため、本当に最後にヴォイスコイルタッチなく動作した時は脱力してしまいました。
3)最後に蝶ダンパーの制動力を落としたので当分この状態で様子を見ようと思いますが、さらに制動力を落とす必要がある場合は、ベークライトダンパー自体を交換するのではなく薄手のプラスチック(コンビニ弁当の透明のフタ等)を切ってベークライトダンパーの内周と外周の間に橋渡しをして接着し、元々あったベークの橋渡しの部分を切り落としてしまうこともできるのではないかと考えています。
4)コーン紙に使った渋紙は#10という厚み(160μm)ですがこの口径に対しては少し薄いかもしれません。幸いエッジがないため外周部に引っ張られることがないのでコーン紙変形による再生上の問題は起きていません。また厚くすると重くなり音離れが変わってしまう可能性もあるので、これもこのまま様子見です。
5)今回はフィールド供給電源を手持ちのMagnavoxと共用したかったために高電圧・低電流タイプとしました。結果、フィールドコイルに使用したエナメル線径はヴォイスコイルと同じφ0.18を選択しました。1kgの銅線をφ0.18にすると4,000mを超える長さになってしまいます。設計に自由度があるならば太いエナメル線を使って巻きの回数を減らした方が作り手は楽ができます。
6)スピーカー用のパーツはフレキシブルワイヤーだけで後は汎用材の使用です。たった1回フィールドコイルユニットをばらして修理した経験のみの人間が、無謀にも設計から材料選定、製作まで1人で行いましたが一応の結果を得ることができました。いろいろなサイトにユニットを自作する方が投稿されており、その方々の情報の助けがなければここまでたどり着くこともなかったかもしれません。自分の記事も少ないとは思いますが、これからスピーカーユニットを作ってみたいというオーディオ絶滅種の方に少しでもお役にたてればと思います。
設計の間違いを途中修正しながら進めましたので、今度作ることがあれば以下の点は修正したいと思っています。。
修正箇所
1)ヨークのフロントサブプレートの廃止。3mm厚×2枚のサブプレートを廃止してトッププレートの厚みを9mmから15mmに変更する。
2)ヨークのフロント以外の他のプレートの厚みを9mmから12mmに変更する。
3)上記2)に伴い穴位置を変更する。
以上をもちまして昨年後半から続いてきました一連のスピーカーユニット設計・製作に関する記事を終了としたいと考えています。
※箱か平面バッフルを作った際にはまた記事にする予定です。
コメント